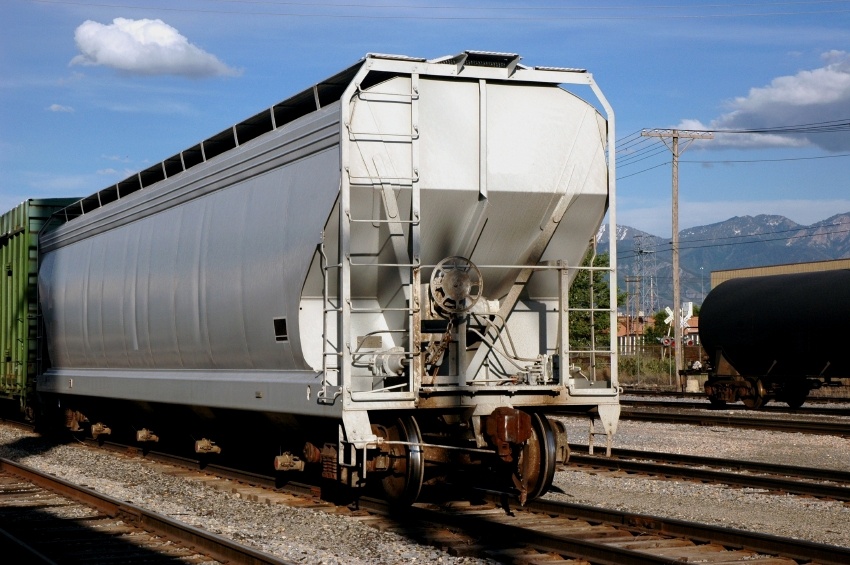
Providing a safer work site for your employees is essential to reducing the risk of accidents, increasing throughput and maximizing your business’s bottom line. Failing to take proper rail safety precautions may lead to serious consequences including deaths, injuries, OSHA fines and other legal ramifications.
Rail hopper cars are used to transport dry bulk commodities, such as flour, sand, plastic pellets, sugar and grains. The hatches on top come in a variety of configurations, leading to spotting challenges that make it difficult to protect your workers. Additionally, chutes and other loading equipment may create obstacles that prevent safe access.
Many injuries and fatalities have occurred after workers fell from the top of rail hopper cars. Adequate fall prevention strategies may have prevented many of these accidents.
Here are three tips for preventing accidents on rail hopper cars:
1. Install Rail Safety Solutions
Installing rail safety solutions is an important step in reducing the risk of injury at your work site. Due to the wide range of hatch configurations and setups of hopper cars, you should work with a trusted vendor that can help you install custom safety equipment for your exact needs.
Common rail safety equipment for hopper cars include:
- Safety cages
- Loading/unloading racks
- Loading silos
- Gangways
- Tie-offs
2. Conduct Safety Training For Workers
Rail hopper car loading and unloading are dangerous when employees don’t know how to use equipment correctly. If an employee is injured while using equipment they have not received training on, your company is at risk of a lawsuit.
Implementing fall prevention equipment isn’t effective if your employees are unfamiliar with proper procedures for using the equipment. It’s essential that you train your employees on how to safely use all equipment necessary for their jobs.
The most successful companies gather input from employees before installing equipment or implementing new procedures. Since your employees are working on the front lines of you facility, they often know about areas of concern and even ways to improve workplace safety.
Once you have refined your safety procedures, be sure to conduct regular equipment maintenance and safety audits. When conducting audits, use this inspection checklist from the Federal Railroad Administration as a guide to see whether your equipment meets safety standards. Additionally, check to make sure your employees aren’t finding workarounds for safety procedures, as this may result in serious accidents.
3. Understand The Physical Parameters Of Your Site
Another important aspect of fall prevention is to understand the conditions at your work site. This includes the physical parameters and the actual processes used at your loading and unloading site.
Train your operators on the logistics and flow of your site as well as the proper safety procedures for working in different weather conditions. This information should be communicated to your employees and your vendors.
Rail safety solutions are only effective when you’re committed to maintaining a culture of safety at your company. Reinforce safety procedures and encourage your employees to provide feedback, suggestions and even criticisms to help you build a safer work site.
Learn more about fall prevention strategies and improving rail safety by watching this free webinar from Carbis Solutions.